Welding management, especially the information management part of the fabrication workflow, is traditionally a labor intensive process. When a system is not well designed and implemented, data that are not captured and human errors when entering data could prove costly for fabricators.
A large investment in a software program need not necessarily ensure that the systems that work around it are followed at all times.
In this article I will show you how you can digitise your welding workflow and quality management system inexpensively and ensure that the system stays implemented with QR code labels, mobile app and the instant messaging features in WeldTrace.

Availability of Information
It goes without saying that essential information must be available to all those who need them at times when they need them.
Like for example, the shop supervisor needs to have access to the welding procedures that will be used in a job and must know which of the welders are qualified for those procedures and are current, in terms of continuity.
The welding inspectors need to know the specifications, both code requirements and client specs, to classify the defects.
Similarly, the welding coordinators need to know the NDE requirements to order tests and set acceptance criteria.
Welders and boilermakers need access to fabrication drawings, weld maps, MTCs or at least the heat numbers for the materials that would be used and perhaps the calibration status of the equipment they would use.
The fabrication or shop manager must know the status of the jobs, so the finished product could be processed further, next set of work could be lined up and so on.
So, it is essential that these need to be in digital form and in a central repository of data that is accessible and that is always updated. This digital data repository will be one source of truth that everyone would turn to and it should keep track of changes, like who updates what, when and so on.
That would rule out Excel spreadsheets as accessing them in the shop would be difficult and it can't keep track of changes. Moreover, it can't store all the files, like drawings, specifications, WPS and the like.
Software programs offered by welding equipment manufacturers are very expensive. If you need to give access to all your fabrication team, the per seat cost will be prohibitive for most small and medium sized fabricators.
There is a relatively inexpensive solution in WeldTrace that you can use to not only digitise build your welding workflow or quality management system. Digitisation now doesn't have to be an expensive affair.
How easy is it to find data?
A digitised welding management system should also be easily accessible and easy to use, especially easy to find information. If your team members cannot easily find what they are looking for, they are less likely to ask someone or put in that extra effort of finding it. So, if everyone should follow a system, that system should be easy to use and the data, be it drawings, WPS, welder qualifications or a traveler, should be right at their fingertips.
In WeldTrace you can upload drawings, MTCs, test reports as well as other documents. All of them are stored in neatly arranged repositories and are easy to find. There is a search function in each of those modules.
You can also digitally create a weld map on a drawing and automatically create welds from that process. The digital lifecycle of a weld joint can begin from your computer. There is no need to use expensive software like Bluebeam that you cannot use to manage welding workflow.
You can also generate QR code labels for welds and affix them next to the welds. Welders can use the WeldTrace mobile app and scan the QR codes and get right to the weld's detail page. From there they can access all the weld data and the weld map, drawing, weld type, WPS, MTC and if they had completed the weld, claim it as well. Imagine how much of data entry can be avoided and how you can also save on labor and keep the information up to date.
The welders can also view their qualifications and their status in terms of continuity for the processes they had qualified.
Similarly, the welding inspectors can perform fit up, record welding parameters and complete the post weld visual inspection and even take a photograph of the weld using the mobile app.
Costly errors in data entry as a result of poor handwriting, missing bits of paper or files, people who can't recall what they had done if you need to find out who did what even a couple of days later can all be avoided by empowering your staff digitally.
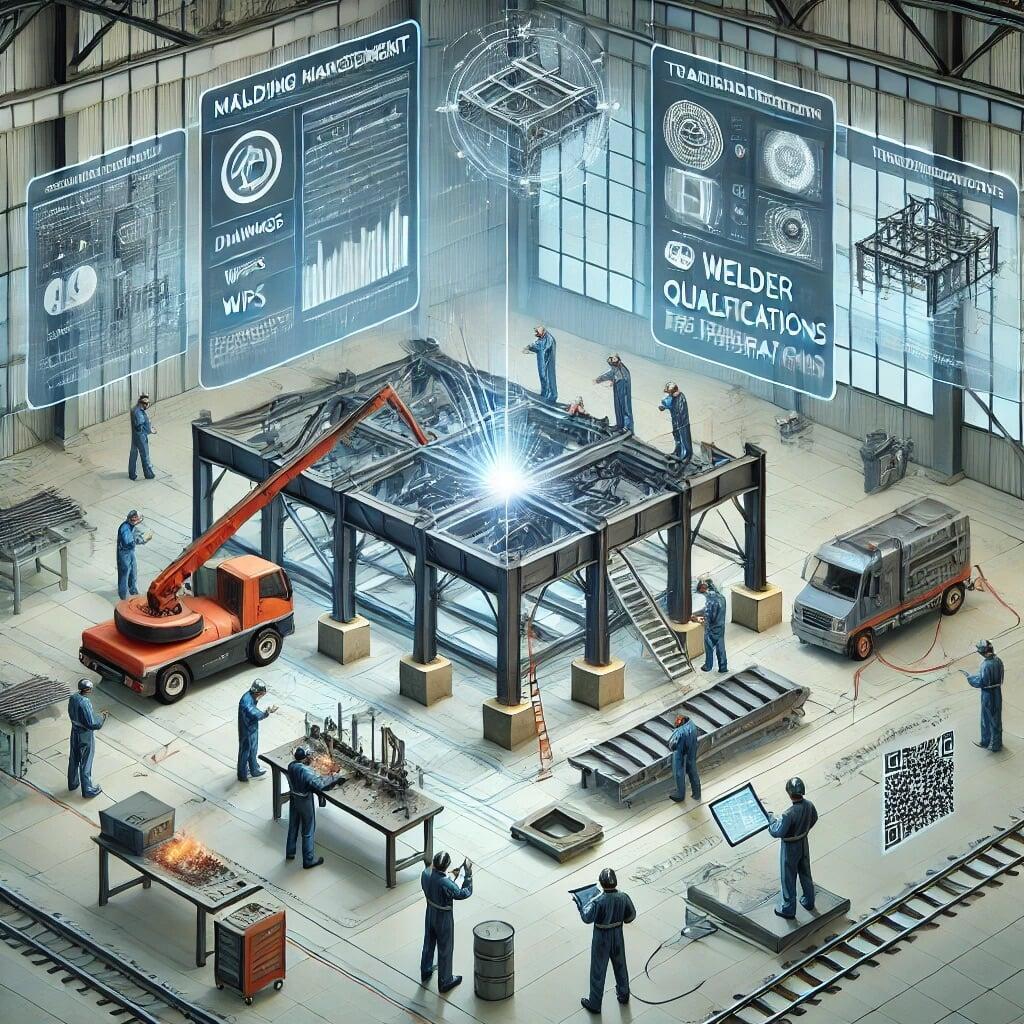
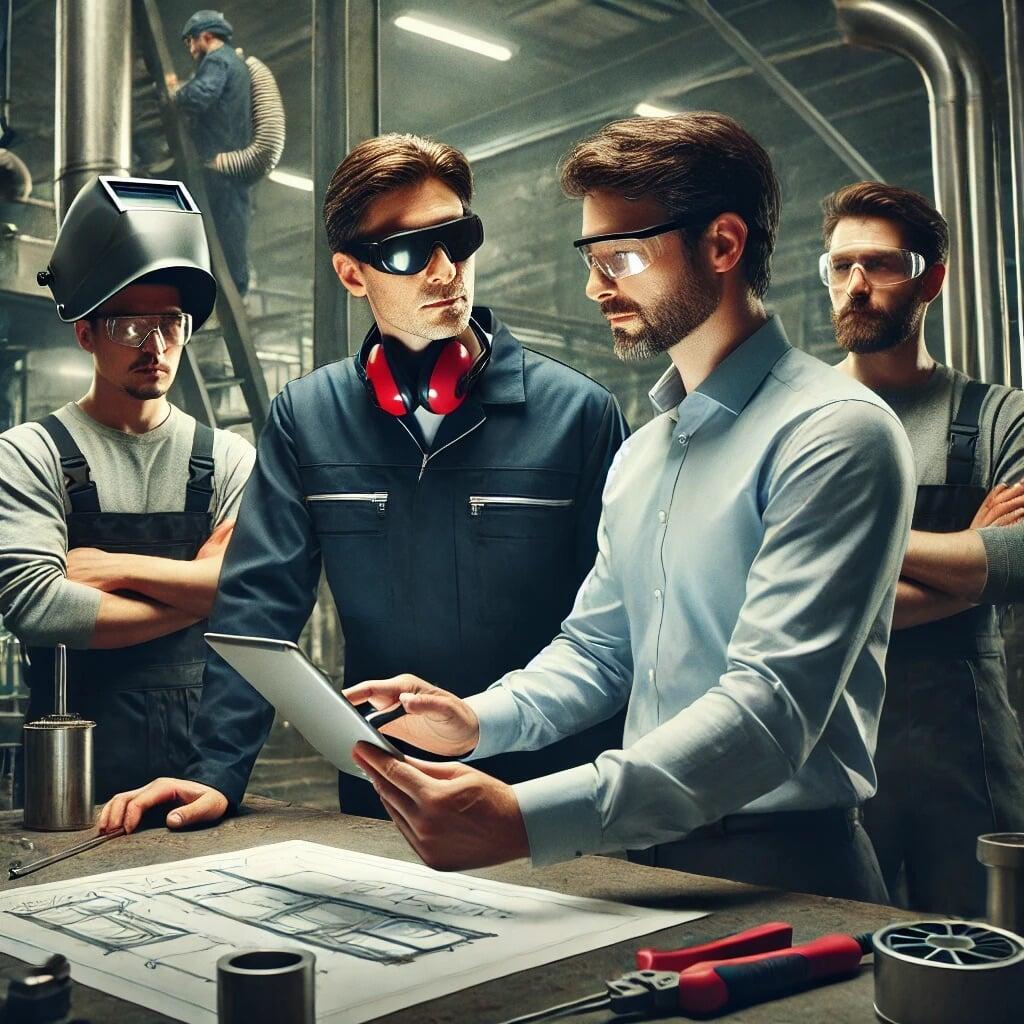
Information Exchange
A digital information system should also facilitate easy exchange of information between the different team members. Meetings are time consuming and they remove people from their work spot. To improve productivity and efficiency, information exchange, like raising a question and quickly getting a reply, sending a status updates, getting notified are all essential.
That is why we built an instant messaging module in WeldTrace. Just like the popular instant messaging apps like Whatsapp, team members can send messages to others from within a weld's detail page.
The mobile app will push the notification to the person to whom the message is sent and they get notified and can respond immediately.
The messages are saved and can even be printed if required.
A fast turnaround for queries will not only improve the operational efficiency, but it will also result in a better adoption of the system and bring faith to it.
WeldTrace can be that ecosystem you always wished that you had.
Updating data is labor intensive
Welding project and quality management inherently are labor intensive processes. Someone has to plan the weldments, allocate welders to jobs, mark them as completed, ask welding inspectors to inspect the joints, coordinate with the testing agencies for NDT, update the weld logs with results.
Invariably, in a small fabrication facility, it is the responsibility of one person and in larger facilities or in large projects, these tasks need to be performed by multiple people. The tasks are usually repetitive and even with the best of intent, human errors are unavoidable and such mistakes could be very expensive.
Data entry is also hated because of its repetitive nature and a third person entering data means additional labor which is expensive. If the data is not captured right at the time, it could be lost.
So, those who perform the tasks should be allowed to enter or digitally capture that activity right then and there. The system should also make that process easy.
WeldTrace has a built in workflow that pushes the fabrication process in steps like planning, allocation of WPS and welders to a weld, marking a weld as completed, inspected, ready for testing, tested, etc. Every activity is recorded and is completely auditable.
Welders, welding inspectors and supervisors can use the WeldTrace mobile app to scan a QR code label generated in WeldTrace to quickly access the details of a weld joint and update the data, saving time and keeping the data real time.
As WeldTrace is hierarchical and built with access control restrictions based on roles, only those roles that are allowed to perform certain activities will be able to do so. This will prevent the system getting manipulated and your customers will have full faith in your process as well as data.
Intelligent digitisation that leads to improved productivity, morale and best of all peace of mind to all the team members doesn't have to be expensive or hard to implement.
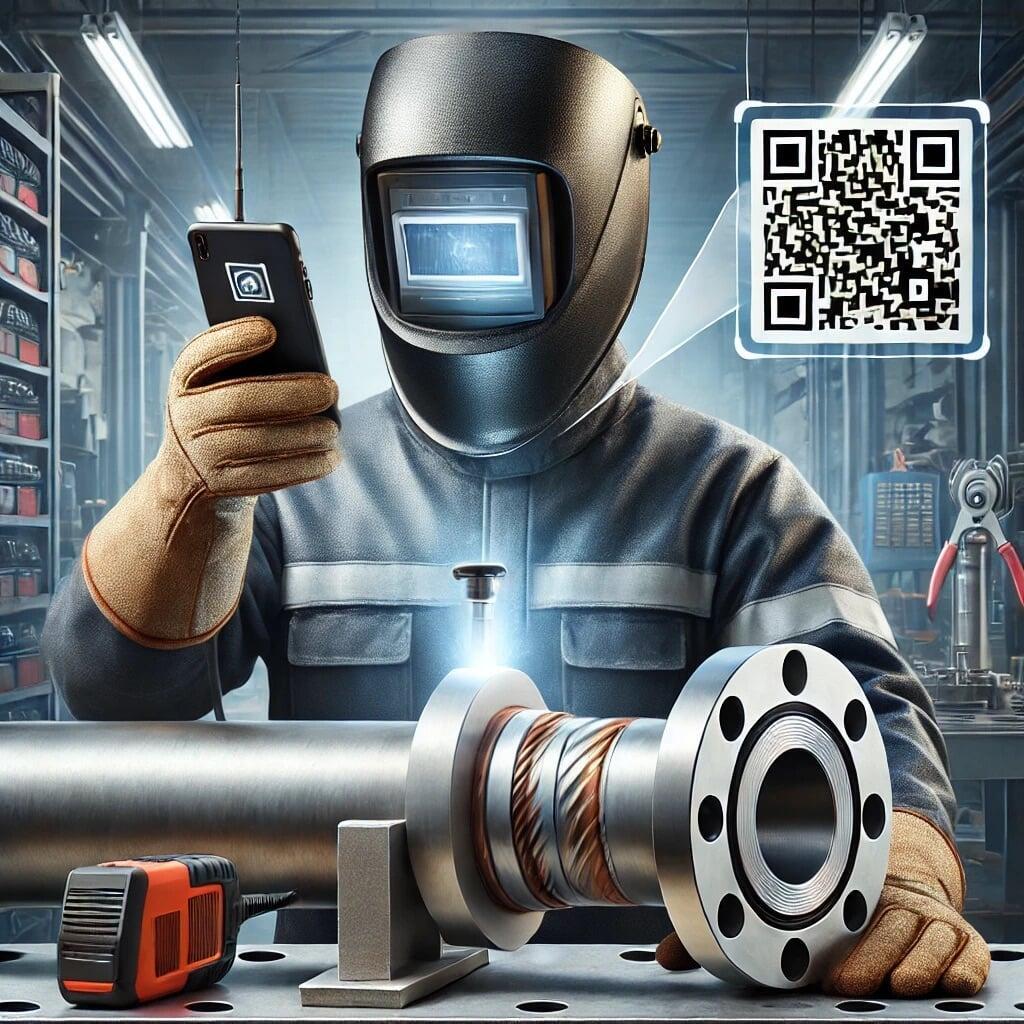

Analytics
Digitisation can bring rich rewards as you can learn from the data that is captured. That is if the data is presented in charts, graphs as well as in raw form, so you can slice and dice it to find where your system is performing well and where it is not.
Digital technology has advanced so much, it is not only easily accessible, it has also become incredibly cheaper in the form of cloud based software such as WeldTrace.
Due to the advent of cloud computing, big data analytics does not have to cost you an arm and a leg. The simplicity of such technology means that you don't need to know anything about data analytics to do it.
We have built WeldTrace with the latest in cloud computing technology that makes performing data analysis so easy. You can run queries with a few clicks and see data such as which of your welder has performed most welds, which one has performed most weld inches, what were the most common defects, how many welds were performed during a certain period and you can imagine every such benefit.
Based on the data you can improve your system and bring credibility and respect to your business.
WeldTrace is so easy to learn and implement, you can hit the ground running if you choose WeldTrace for your digitisation journey. Contact us and we will show you how easy and inexpensive it can be to digitise your welding management system.
These are just some of the benefits of digitising your welding quality management system. WeldTrace will make it easy to digitise your welding management system and at a fraction of the cost of what you may have thought you need to spend.