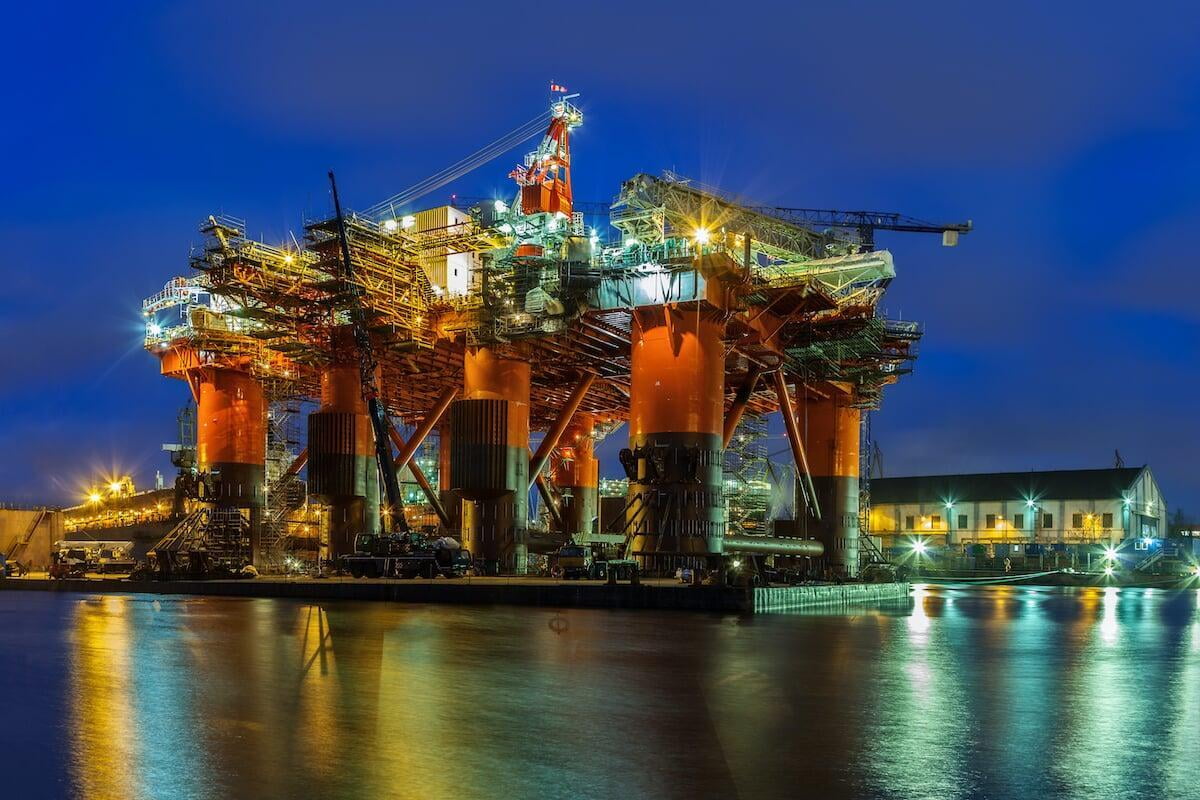
How do you manage contractors & their people?
In large EPC projects you typically find several subcontractors supplying fabricated components. They are mostly spread across different countries, each employing hundreds of welders. The quality culture could vary a great deal. So, you often end up facing questions like these:
- How do you ensure that each contractor maintains their quality system and follows specifications and contractual requirements?
- Are their welders welding to procedures they have qualified in?
- Are their welders in continuity? Are continuity records maintained?
- Are welding records maintained for full traceability?
- How do you even trust if the data they are submitting is truthful and correct? Where is the oversight? Who performs routine audits?
These questions may sound familiar and you may recollect many more when facing audits as the welding manager or quality assurance manager of a project.
You may have tried countless training sessions, implemented written procedures, performed numerous quality system audits, issued non-conformance reports, pretty much to no significant improvement.
So, how do you bridge this vast gap of culture, language, system and other barriers to manage large projects as well as they should be? Please read on.
How do you manage the welding records?
The principal EPC contractor is ultimately responsible for the delivery of the project and its quality. That means taking up the responsibility of managing all the subcontractors and the quality of all their work.
It means managing tons of paperwork coming from different parts of the world at irregular schedules at best and lots of followup to get them.
You miss one record and it could potentially stop your team from going ahead with the completions and commissioning work for a system.
When you have fabricated parts that could each have hundreds of welds, it could mean tracking shop and field welds that may be in the tens of thousands, each with a set of records to account for full traceability.
The records are not limited to welding procedures, PQRs, welder qualification records, their continuity, material heat certificates, consumable batch certificates, inspection reports, NDE test reports, records of repair and retest, weld logs, weld maps on top of the associated as-built drawings, all with proper revision control and not superseded.
If this is what you are looking at the end of the project, imagine how well the project needs to be controlled to ensure that every one of these records are produced and maintained at the right time.
So, how do you manage this seemingly impossible task of managing hundreds of thousands of records? We offer a solution. Please read on.
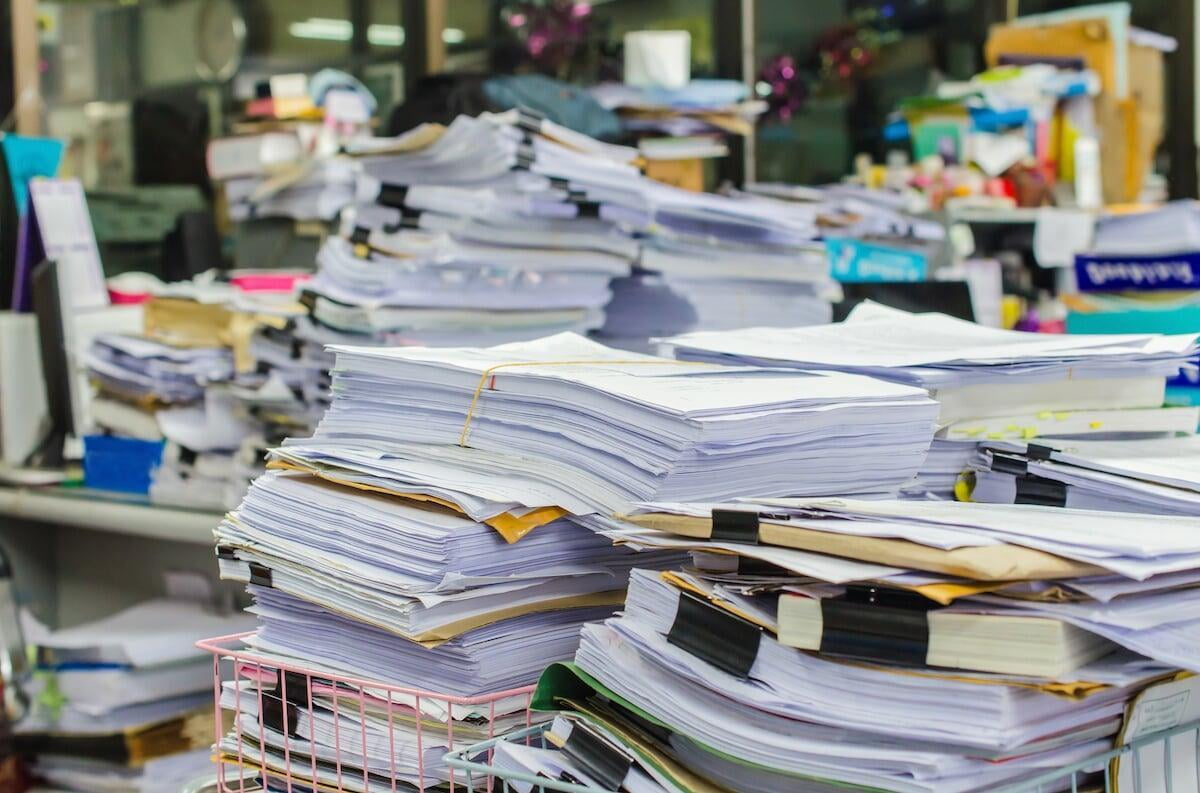
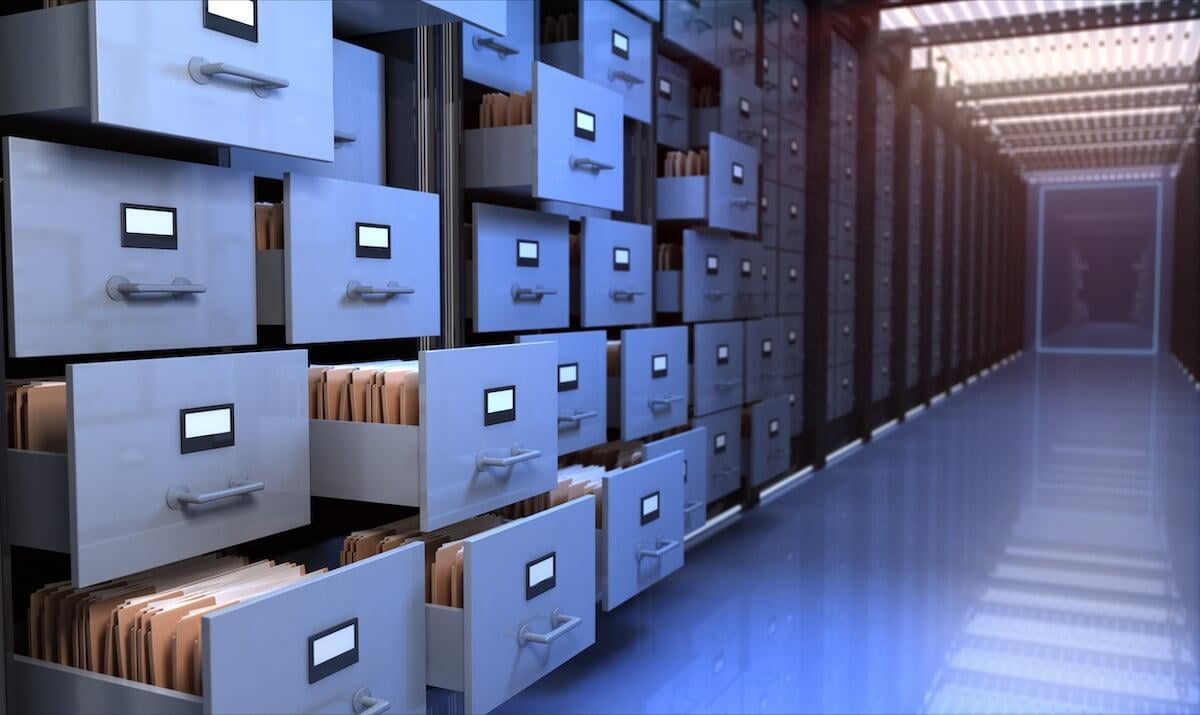
How do you demonstrate welding QA/QC compliance?
Most EPC contractors use Excel or a home grown application to manage weld logs and traceability records. As record keeping for compliance is time consuming, requires diligence and is boring, a vast majority of the staff may try to shortcut the system without realizing their company's exposure to risks.
A decent welding QA/QC or quality audit could expose the fact that records are not kept regularly, personnel doing bulk updates of records for a few days or few weeks at one time, some of them may be erroneous or unverifiable as significant time had passed when the activity happened and when the record was created.
Codes, customer specifications, contractual requirements and the certification standards like AISC, ISO 3834 and ASME require a contractor to keep records up to date.
The system to demonstrate welding QA/QC compliance should be one that the head contractor and sub contractors use all the time and the data is available in near real time as possible. The system should create history or traces of who created or edited which record, the changes made and the data should be preserved for integrity, just like how you would expect internet banking to maintain records of all your transactions.
If the system that you use is not user friendly for the sometimes old fashioned, old school or not so tech savvy people employed in the fabrication industry, there is little hope of demonstrating compliance.
What you need is a system that is proven, reliable, easy to use and more than that your staff must be willing and eager to use on a daily basis. We have the just the solution you are looking for. Please read on.
How do you manage the risk of non-compliance?
Using systems, tools and perhaps a software to create WPS, PQR, welder qualifications and manage weld logs, test reports and the like are one part of what all contractors performing code work need. The other important part is how to effectively use such data and manage compliance and risks.
There are a few software products available to create WPS/PQR/WPQs and fewer still for managing welds and traceability. Due to the lack of extensibility of these products, they only offer limited help, especially for the large EPCs.
As the saying goes, a chain is only as strong as its weakest link. If some of the contractors have very good systems and others not so, the project could be facing risks associated with demonstrating compliance.
The system should be able to handle multiple teams across geographic locations and able to handle a vast amount of data in real time. And it should be easy to use and not be a burden or addition to what the teams do.
The risk of non-compliance to an established welding QA QC system and the eventual cost of repair and remediation is very real. Here's a link from the Australian Financial Review about the situation Chevron's $54 billion Gorgon LNG plant is in: https://www.afr.com/companies/energy/chevron-delays-gorgon-lng-restart-20200903-p55s4k. Cracks in welds are costing Chevron hundreds of millions of dollars every month.
So, how do you manage the risks from non-compliance to a welding quality system without micromanaging all the contractors and auditing them countless times? Don't worry. Your answer is WeldTrace.
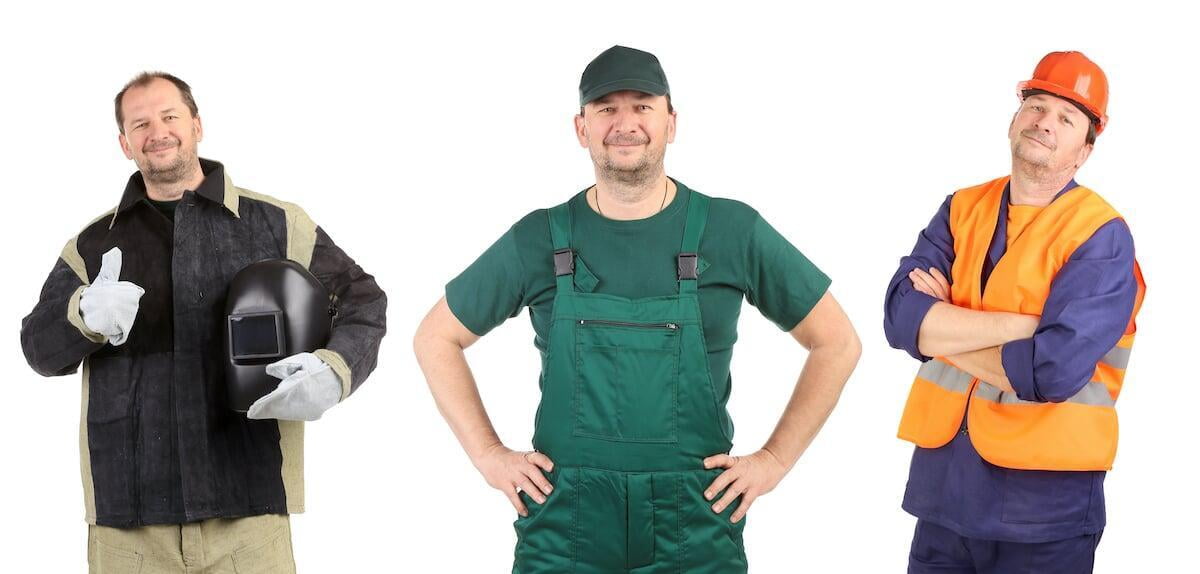
Integrated system for welding
Transform from the traditional and old school way of managing welding projects to the modern and reliable way by leveraging technology. Technology everyone is willing to adopt and use on a daily basis, voluntarily that is. Don't everyone have a smartphone these days?
Imagine how much money and heartache it would save you if only you can get all the contractors use the same platform. A platform that would offer them flexibility to run their projects in the way they want to, yet you have the oversight and have access to data in real-time.
You can appreciate the benefits of an integrated system with everyone on the same page, a single source of truth and what it can do for customer confidence. A system that is extendable and capable of growing with you over time.
The more integrated the system is with the business processes, the benefits in increased productivity, confidence and competitive advantage that it would offer your company would be priceless.
Welcome to WeldTrace, the end-to-end welding management software.
WeldTrace is the end-to-end welding project management software for welding QA QC, quality assurance and compliance
Major features in WeldTrace
One platform for total project management
- Cloud hosted in advanced servers with redundancy - 24x7 access from anywhere
- Use with a browser or tablet or mobile phone - no extra cost for gadgets
- You do not need to connect power sources to servers - WeldTrace is different
- Collaborative, yet compartmentalised data - give access to your account to select few
- Role based and hierarchical access to users - limit exposure to data and what they can do
- Project access privileges are configurable for different roles
- The ongoing cost is just 15 cents per weld (20 cents for the Plus plan)
Welding workflow management made easy
- Built-in workflow for weld lifecycle
- Role based access control
- Plan, allocate, complete, test, inspect
- Visual inspection by stage
- NDE module to request, test, handle repairs, penalty, tracer, sampling
- NDE settings for project and drawings
- Work packs to group welds and plan
- Traveler, control sheet, job card print options for hard copies to the shop
- Instant messaging for communication between project team members
- Welder who is not qualified or out of continuity prevented from being used
- Welder continuity records updated automatically
- Full traceability for each weld
Weld mapping and dimension mark-up interface
- Weld numbers marked up in sequence automatically
- Create welds automatically
- Pick attributes of welds like size, joint or weld type
- View weld map and navigate to weld
- Produce high quality weld map prints
- Edit and move weld map annotations
- Transfer weld map annotations when drawings are revised
Repositories for project data
- Tags to manage fabricated items with multiple drawings
- Drawings with version control
- Materials repository manage heat numbers, MTCs, inventory control
- Filler metals area
- Project documents with version control
- Area to store all the test reports
- Use welding procedures from the WPS module for all the projects
- Welders are stored and managed in a central repository for all the projects
Manage the data with ease
- Forms for editing one weld or other data at a time
- Excel style interface to edit the weld log, hundreds of welds at a time
- Wizards to import and export data
Data analysis
- Project calendar and Gantt chart views
- Progress bars
- Instant messaging between users, notifications and alerts
- Rich dashboard and data analysis tools
Final project documentation or turnover packs, easy!
- Produce turnover packs in a few clicks
- A single PDF file with all the selected documents
- Data shown in tables with links to files
- Table of contents and section separators
- Headers and footers can be customized
- Include only what you need to show
You may visit this site to learn about inspecting and testing welds and about weld defects: https://primeweld.com/blogs/news/weld-quality-testing-guide